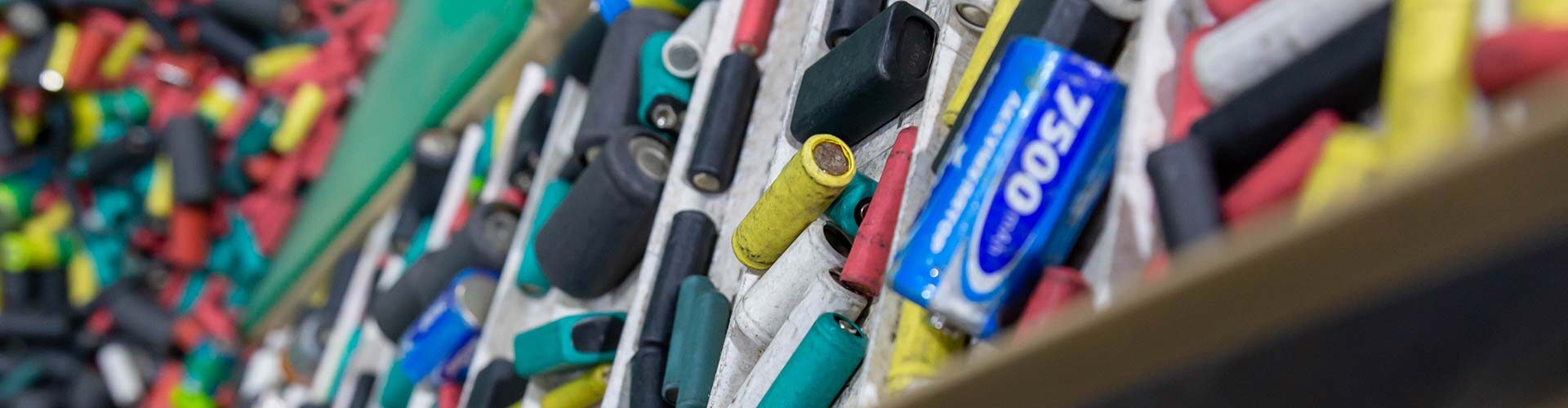
Global Responsibility
Disposing and recycling of used portable batteries has become a global issue as battery consumption continues to rise. There is a growing focus on the proper collection, storage, sorting, and development of recycling methods to minimize the amount of waste and prevent harmful substances from entering the environment and the human body.
In Europe, the Extended Producer Responsibility system requires battery manufacturers or suppliers to pay a fee to a state fund to ensure proper battery recycling. This money is managed by non-profit regulatory organizations, which facilitate the recycling process by coordinating collection and recycling efforts. Many recycling companies prefer sorted batteries over mixed streams for recycling, as recycling a single type of battery costs four times less than for a mixed stream.
Our technology, when utilized in the sorting phase, will enhance the efficiency of the entire process. This will result in a higher volume of recycled batteries and a decrease in recycling costs, thereby reducing expenses across all stages.
Furthermore, it is widely acknowledged that the quality of sorting directly influences the quality of the output from the processing stage. Different types of batteries yield different fractions of substances with varying applications. For instance, heavy metals in fertilizers undermine their suitability for agricultural use. Similarly, impurities in metals complicate and increase the labor required for metallurgical processing. Additionally, it is essential to consider that higher sorting purity significantly lowers the risk of accidents, such as explosions and fires in lithium battery recycling facilities.
Battery Sorting Methods
Currently, there are various battery sorting methods used around the world. These methods are designed to quickly and accurately classify the mixture of used batteries based on their internal chemical composition. They include manual sorting, optical sorting, sorting by weight and electrical conductivity, and magnetic sorting.
The current market offers a wide variety of batteries and accumulators, all of which are classified as hazardous solid household waste. This is due to highly toxic heavy metals, such as mercury, cadmium, or lead, in varying concentrations within their electrochemical cells, depending on the type.
As the literature states, used batteries account for up to 40% of all toxic substances introduced into the environment through household waste.
Certain batteries and accumulators contain higher concentrations of valuable metals like silver, nickel, cadmium, or zinc compared to the levels found in natural ores.
Batteries A Global Recycling Problem
Battery and accumulator production is steadily increasing. It is crucial to prevent toxic heavy metals from entering the environment through household waste and to utilize raw materials from used batteries or accumulators in the metallurgical industry. This makes collecting, sorting, and recycling batteries and accumulators an important issue.
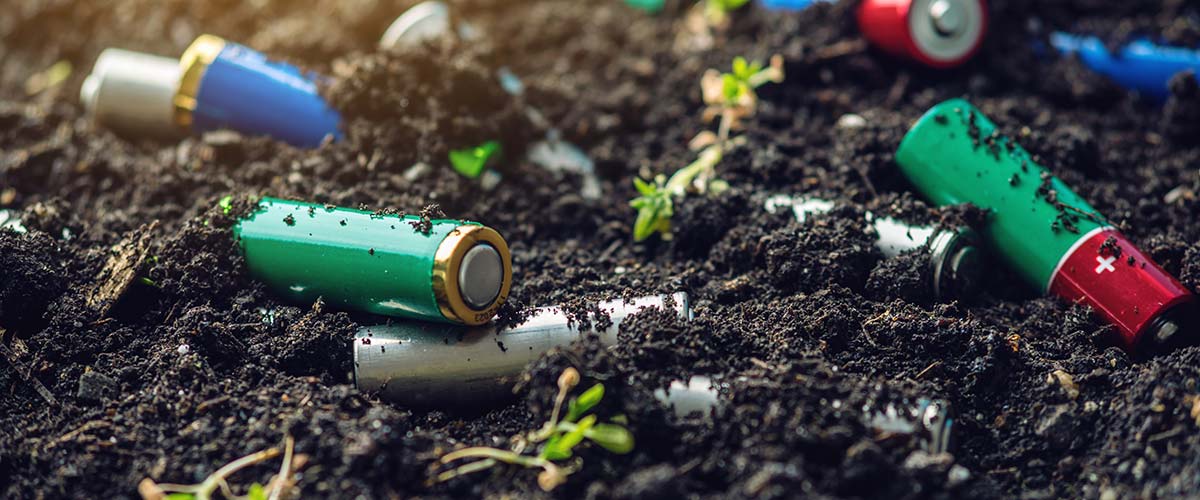
European nations have a longstanding commitment to addressing battery recycling concerns, with battery collection rates steadily rising.
Close to one-half (48%) of the portable batteries and accumulators sold in the EU were collected for recycling in 2021. And in the U.S. (2023) the lead battery industry continues its outstanding recycling rate of 99%.
As per estimations by Fraunhofer ISI, the quantity of batteries in line for recycling in Europe is expected to reach 420 kilotons by 2030 (with a scenario range of 200-800 kt) and 2100 kilotons by 2040 (with a scenario range of 1100-3300 kt).
Most industrialized nations have established infrastructure for separate waste collection, with designated collection points for used batteries located in public areas. Consequently, the collection containers contain a mixed assortment of waste batteries and accumulators with diverse types of electrochemical cells.
To recycle valuable metals and materials in the industry, it is necessary to have a sample of batteries with a high purity level (over 95%). This means that old batteries and accumulators collected in containers must be sorted based on their chemical composition.
LINEV Group sorting solution for batteries using X-ray technology
Since 2017, the employees of LINEV Group have conducted several research studies to establish the feasibility of utilizing X-ray technology to identify and sort different types of used batteries. They have also focused on selecting the main components and the optimal operating modes of the system. Utilizing the internal structure of the batteries, each specific type exhibits distinctive areas that can be automatically detected via X-ray.
What makes X-ray technology unique and advantageous? Our technology has the capability to see through the batteries, solving the problem of identifying batteries even in cases where labels are missing, markings are obscured, or there is rust.
Furthermore, the global market often faces the issue of counterfeit batteries produced by dishonest manufacturers, where the battery composition needs to match what is stated on the label. Neither the human eye nor any optical system can detect this discrepancy, potentially leading to sorting errors with adverse consequences. In contrast, X-ray technology does not rely on the label. If the recognition algorithm determines that a battery is NiCd-based, it will not place it in the group with metal hydride, regardless of the markings. To ensure precise categorization of batteries and accumulators, we have developed a process for identifying and classifying their characteristics in X-ray images. Additionally, special algorithms have been created to recognize and sort all household cylindrical batteries of standard sizes into five different types.
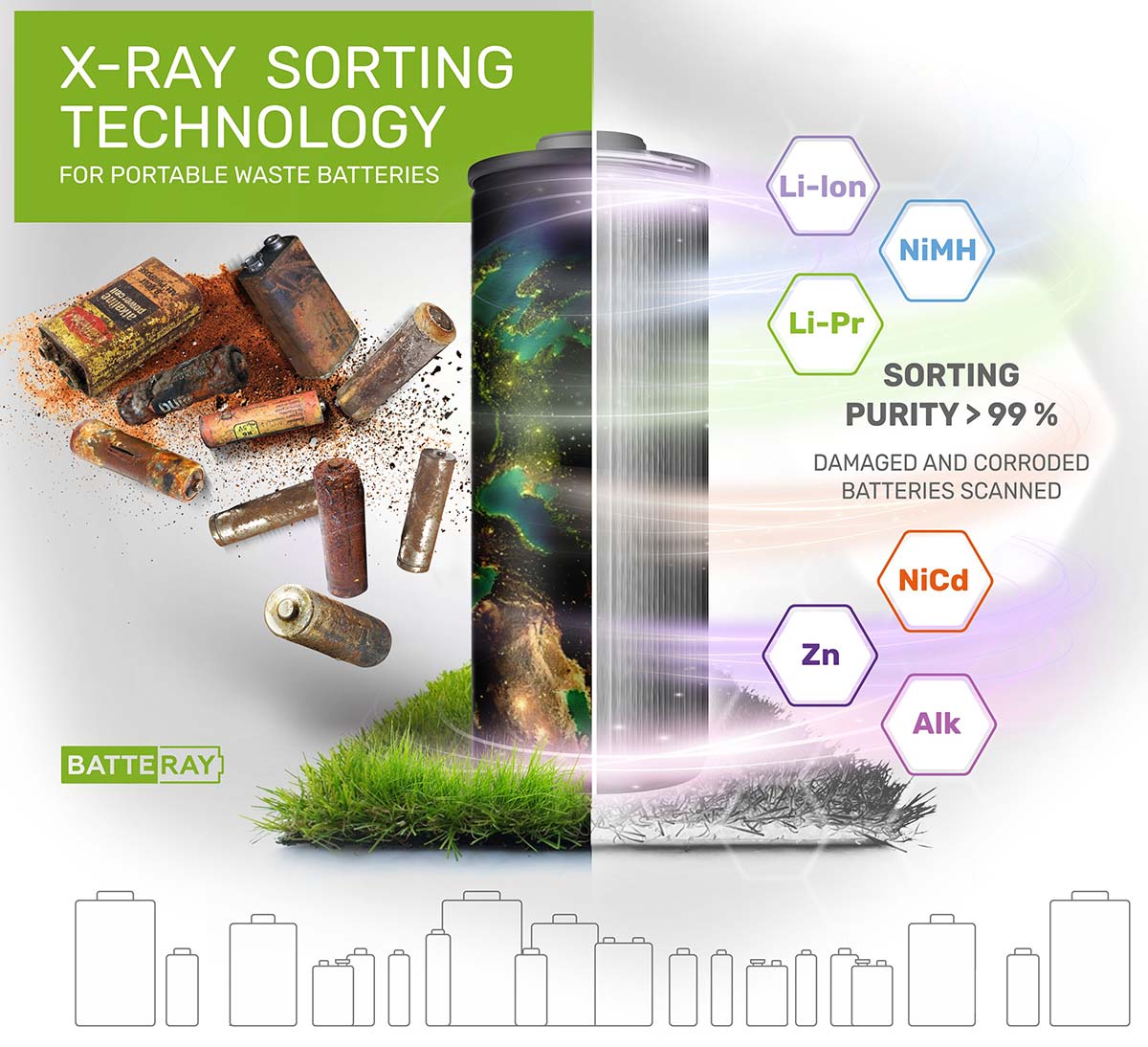
The sorting process is entirely automated, removing any potential influence of human error and eliminating the need for manual labor in a process that can be harmful and hazardous to health.
Integrating a conveyor system design with an advanced algorithm for battery recognition using machine vision and artificial intelligence, enables the rapid and highly accurate sorting of batteries. The sorting accuracy for the most commonly used types, alkaline and saline, exceeds 99%.
The standard sorting list comprises commonly used types and sizes of batteries, such as Zinc-carbon (salt), alkaline, nickel-metal hydride, nickel-cadmium, and lithium. However, users have the flexibility to incorporate their own standard sizes by utilizing the system’s self-learning module.
BATTERAY — Innovation in Action
In our opinion, the commercial solution of our product, the BATTERAY system, comes with the following key advantages:
- The battery-feeding hopper can be customized to accommodate different sizes based on the processing line’s throughput at the facility. Similarly, the sorting conveyor can be adjusted to adapt the necessary number of battery types.
- We have developed a dedicated conveyor system for removing small debris, ensuring that only clean individual batteries are scanned. This process eliminates any small debris, electrolyte dust, battery fragments, and small button batteries, resulting in accurate sorting and cleaner substance fractions.
- Operators are entirely protected from the potential risks of ionizing radiation, as the system is designed by European safety standards, eliminating any concerns about radiation exposure.
- Our system is equipped to operate effectively in challenging weather conditions, including hot and humid environments in various countries.
The application of X-ray technology in battery testing extends beyond sorting portable batteries. With the increasing production of batteries for electric vehicles, our technology streamlines the process of product quality control, enhancing its reliability. We are prepared to face new challenges and tasks in producing and processing batteries as a team.
Our system is ready to new unknown challenges in the field of battery processing.